Keeping an industrial facility running smoothly and safely requires constant attention to detail. Our client, a broad energy company that produces and markets fuels, natural gas and electricity worldwide achieves this by retaining a host of skilled and competent service providers. They perform diverse technical tasks in a set of high-risk plants located throughout Belgium.
Context & challenges
Each of them have their own risk sensitivities. So the work permitting process needs to cover a wide range of eventualities. The document at the heart of the relationship between client and service provider outlines the various hazards and risks inherent in either the work itself or the job site. Moreover, it coordinates the practical measures that must be taken to mitigate these risks and avoid incidents. In short, it entails the accident prevention plan that must be follow by an outside company working within the facility, as well as the client’s responsibilities towards that company.
Moreover since they can be valid for either a discrete work project or for a period of time (e.g. weeks or months), multiple work permits are usually issued against them. Over time it had become complex, and because the underlying documents were paper-based, it was difficult to optimize. Whether for critical maintenance on a hazardous goods storage tank or to fix a toilet, the basic process was as follows:
- Tenders are solicited; a service provider is chosen
- An overarching framework agreement is written that outlines the work, risks and hazards present at the job site, rules governing the contractor’s activities, and the responsibilities of the client toward the contractor
- Individual work permits detailing scope and location of labor are issued for daily work crews; on average 2,500-3,000 work permits are generated annually
While the process itself was sensible, it had an inherent flaw while it was still paper-based. It means this crucial information doesn’t always get transferred over. In the end, neither our client nor its contractors were well served by this manual process, which had become very complex over time.
Our approach
Our client was looking for a completely new approach to archiving and producing this documentation. A new digitalized system that would not only save time and reduce administrative overhead but would also stop the information gaps promoted by the old, cumbersome documentation process.
In order to answer our clients challenges, we collaborate with Otofacto to analyse its need in the first phase. Then, our team from our Web & Mobile Delivery Center developed a fully customized paperless system:
- Cloud-based and built on a Progressive Web App Platform. While this approach came with slightly higher upfront costs there are, now, no future licensing or renewal fees.
- Clean and user-friendly web interface that ensures all the right information is gathered when forms are created and signed.
- Proprietary software in the back end, password-protected web access on the front end. The contractors are provided password-protected web access to a portal where they can manage the documentation for their own projects.
- In order to support the adoption of the platforms by the employees, we ran several training sessions for them.
All documents are created and managed online: framework agreements, supplemental documentation, work permits… everything. Moreover, since digital documents can be linked to without limit, now it’s possible to write framework agreements that cover multiple facilities.
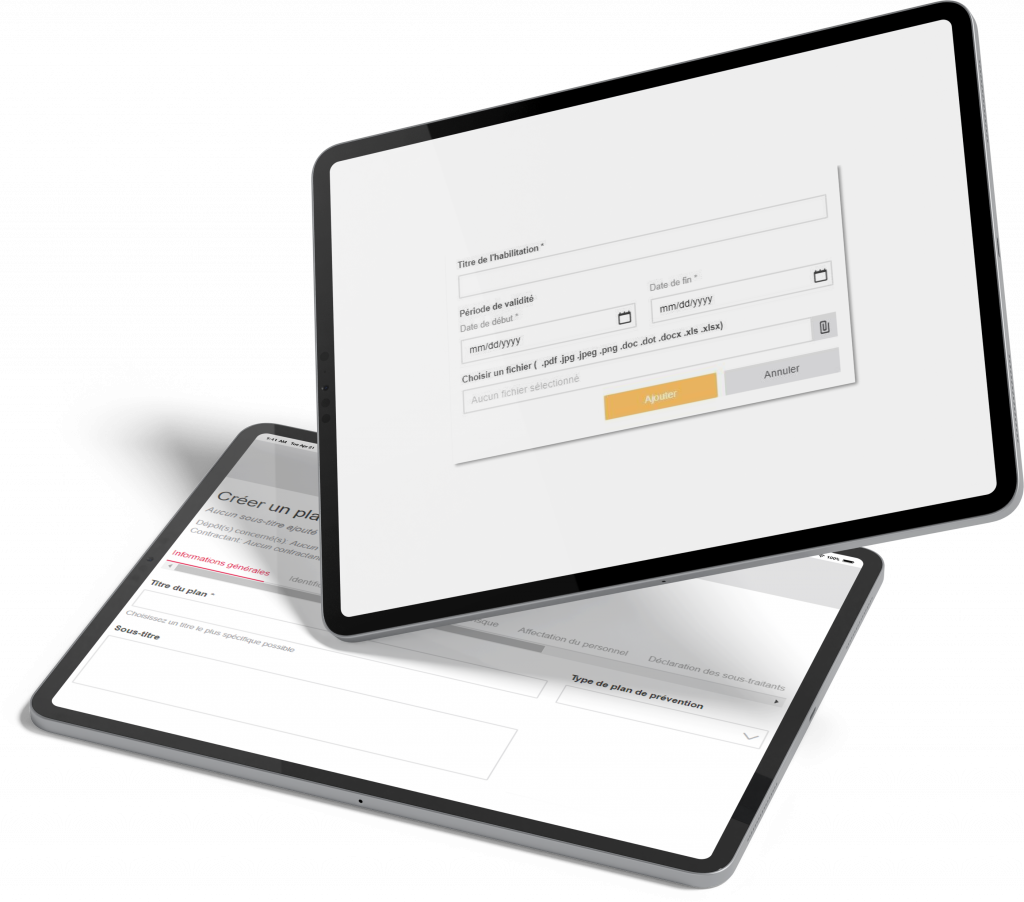
Benefits
The solution from our product team is well beyond the obvious savings in time. Benefits of the new system include information transparency, process simplicity and flexibility.
It has also greatly enhanced awareness of critical, legally-binding work requirements on the part of its contractors. Now, when an administrator creates a work permit, it is necessarily linked to a specific framework agreement.
The relevant information then automatically populates the corresponding form fields in the work permit. It means that, on the day of work, the contractor’s employees sign and receive a copy of a work permit that actually contains all the relevant content from the prevention plan, as well as any other relevant documents that pertain to the job or the job site.
While issuing the work permit, the system also checks whether, for example, two different contractors are scheduled to do work in the same physical space at the same time. Whereas previously, this was also a manual process.
In a nutshell, thanks to this platform our client is able to:
- Completely digitalize a cumbersome, paper-based process for creating and archiving framework agreements, accident prevention plans and the thousands of work permits issued yearly.
- Save time and effort, reduce errors in creating work permits and ensure that documentation procedures are followed.
- Easy information transparency: overview of work permits, including information on the hazard level of the work.
- Administrative view provides high-level information about the client’s maintenance and repair activities across its facilities.
- Potential work conflicts – different contractors working at the same time in the same place – are raised before issuing work permits; the permissions process when work proceeds despite the alert is tracked and documented.
- Work permits issued on the day of labour now include critical risk mitigation information taken directly from the prevention plan as agreed by client and contractor.
- Web access and cloud storage provides new flexibility on the go; offline mode ensures that some functions are still available even if internet connectivity goes down.
- Easy information transparency: the client’s web interface provides a system administrator with access to KPIs such as the number of framework agreements created over a certain time period, which site(s) they pertain to and a breakdown by type.
Technologies & Partners
Global Delivery Model
- Client’s Location: Brussels
- Delivery centers: Web & Mobile EU
- Ecosystem brands: Positive Thinking Company & Otofacto
Discover how we help you bring your product vision to life.
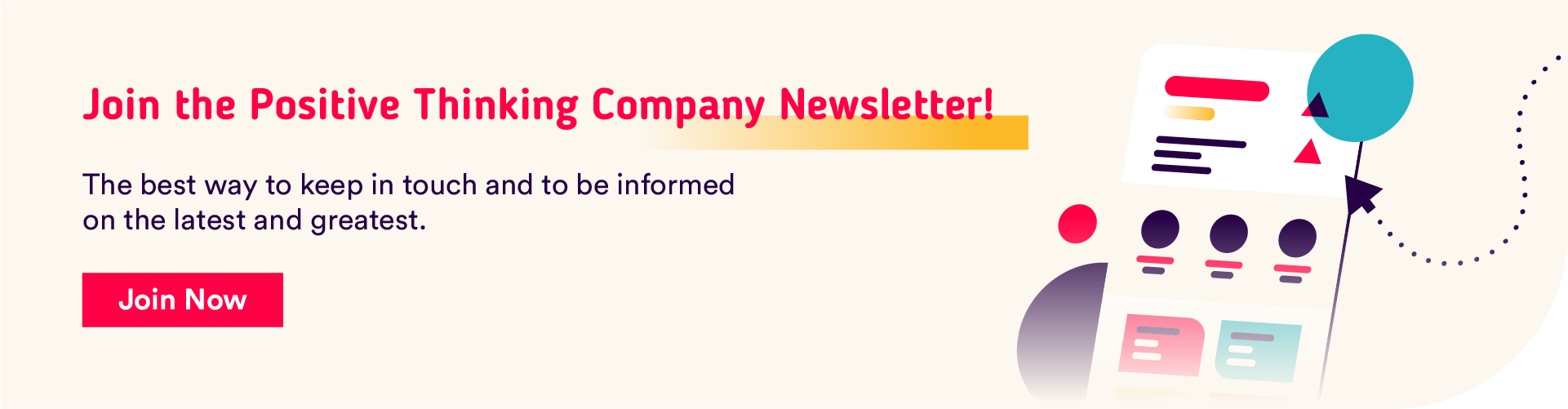